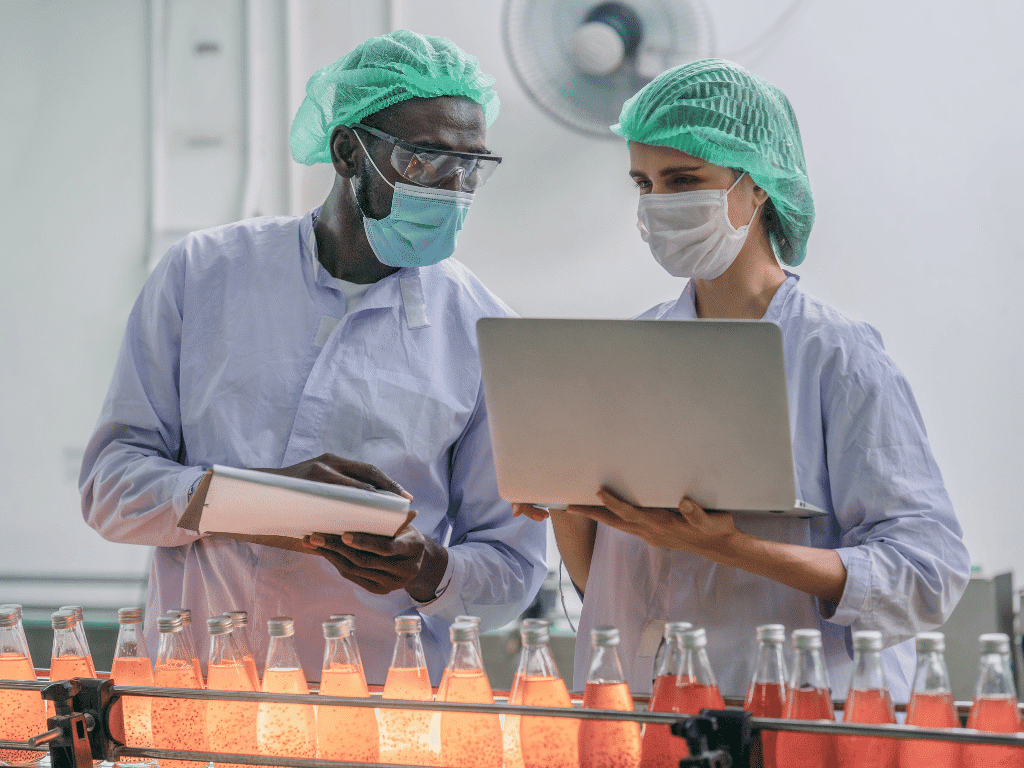
Effective work order management serves as the backbone of a manufacturing site, ensuring the seamless flow of processes that are interdependent in finalizing a batch or production phase. Despite its critical role in enhancing productivity and agility on shop floors, many factories still rely on outdated and decentralized systems for work order management, posing challenges for executives in tracking production steps effectively.
This article is designed to inspire manufacturing executives by offering insights into work order management in the era of Industry 4.0. We begin by breaking down the steps of work order management, highlighting digital tools that have the potential to enhance each stage. Additionally, we provide best practices for work order management to assist manufacturers in optimizing the smooth flow of tasks.
What Is Work Order Management?
Work order management is the systematic process that oversees the lifecycle of tasks and work orders within a manufacturing environment. It involves the organization and coordination of various activities necessary for the production of goods.
A work order can be defined as the major steps in the production process. In pharmaceutical manufacturing, for instance, granulation, encapsulation, or packaging can be designated as work orders. Alternatively, the setup of a machine or the cleaning of the production line within the packaging process can also be considered work orders, and these definitions may vary from one factory to another.
Nevertheless, work orders are interdependent processes, making them challenging to organize optimally. For example, granulation must be scheduled before packaging, or setting up a machine must occur before running a specific work order. The interdependence of these tasks creates constraints that executives must consider for effective work order management.
In this context, Industry 4.0 technologies play a crucial role. Analytics, heuristics, and algorithms empower managers to make augmented decisions considering these constraints.
8 Steps of Work Order Management
1. Task Identification
Identifying tasks is the foundation of effective work order management. This involves a thorough analysis of the production requirements, resource availability, and timelines. Digital tools like task management software can aid in creating a comprehensive list of tasks required for the manufacturing process.
2. Establishment of Work Order
Once tasks are identified, the next step is to formalize them into work orders. This involves detailing the specifics of each task, including materials needed, machinery involved, and any relevant instructions. Digital platforms can facilitate this process, providing a centralized repository for work orders.
3. Priority Evaluation
Assigning priorities ensures that critical tasks are addressed first. With Industry 4.0 technologies, manufacturers can utilize real-time data to dynamically assess and adjust task priorities, optimizing resource utilization and meeting production deadlines efficiently.
For instance, manufacturers can prioritize a customer with a low OTIF score. Or by evaluating the schedule adherence metric, executives can decide which work order to complete first.
4. Scheduling Work Order
Creating a well-structured schedule is crucial for maintaining a smooth workflow. Scheduling step includes distributing work orders to production lines and assigning work orders to specific laborers.
Modern Advanced Planning and Scheduling (APS) tools automate these steps through AI algorithms and heuristics, enabling optimal scheduling while considering interdependency constraints, skillset of workers and various objectives such as changeover minimization, just-in-time delivery, cost minimization, and more.
AI schedulers also facilitate real-time adjustments and provide visibility into the entire production schedule.
5. Execution of Work Orders
With work orders assigned, the execution phase begins. Gathering real-time automated data through IoT devices sets the core for production tracking, where unplanned downtimes can trigger notifications for maintenance staff and operators to take necessary actions.
Beyond collecting factory data, displaying it on automated dashboards that provide granular information on the line or even station level (see image below) allows line leaders and executives to monitor production 24/7 and take agile actions against the bottlenecks that slow down processes.
6. Documentation of Completed Activities and Tasks
Accurate documentation is vital for quality control and compliance. Digital documentation tools such as digital logbooks (see image below) and digital batch records enable real-time recording of completed activities, ensuring transparency and providing a comprehensive record for future reference.
Digital documentation tools that ensure ALCOA+ data integrity principles are crucial for heavily regulated industries, such as pharmaceuticals. Organizations like the FDA issue warning letters to manufacturers for non-compliance with cGMP. According to SCW.AI’s analysis, utilizing paperless quality tools reduces the chance of receiving warning letters from the FDA by 8% in 2023.
7. Closure of Work Order
Closing a work order involves verifying that all tasks are completed satisfactorily or reporting the root cause of potential failures. Digital verification processes and quality control checks help in ensuring that the manufacturing process aligns with the established standards before closing the work order.
8. Data Analysis for Continuous Improvement
After production, data analysis becomes instrumental in identifying areas for improvement. Leveraging analytics tools allows manufacturers to gain insights into the entire work order management process, enabling continuous refinement and optimization for enhanced future performance. Waterfall analysis (see image below), OEE reports, takt time analysis, and more can help the management team identify chronic bottlenecks on the shop floor by analyzing historical factory data.
5 Work Order Management Best Practices
1. Utilize a Centralized System
Implementing a centralized system ensures that all stakeholders have access to a unified platform, promoting transparency and collaboration. This system should serve as a hub for creating, tracking, and managing work orders. With a centralized system in place, executives can efficiently oversee the entire workflow, reducing the chances of miscommunication or information silos. Nowadays, cloud-based factory platforms offer the flexibility and accessibility required for real-time collaboration among team members across different departments.
2. Harness APS Systems for Automated Activity and Task Assignment
APS systems powered by AI are invaluable for automating the assignment of activities and tasks within work orders. These systems take into account various factors such as resource availability, interdependencies, and production objectives to optimize task allocation.
By leveraging APS systems, manufacturers can enhance efficiency, minimize manual errors, and adapt dynamically to changing production requirements. The result is a more agile and responsive work order management system that aligns seamlessly with Industry 4.0 principles.
3. Prioritize Work Orders With Color Coding
Color-coded prioritization is a simple yet powerful technique to enhance visibility and responsiveness in the fast-paced manufacturing environment. For instance, high-priority work orders may be assigned a distinct color, making them easily distinguishable on scheduling dashboards. This visual approach aids executives in making rapid decisions based on real-time data, contributing to better resource utilization and meeting production deadlines.
4. Assign Workers by Considering Workers’ Skills
Efficient workforce allocation is crucial for optimizing the execution of work orders. Instead of assigning tasks arbitrarily, consider the skills and expertise of individual workers.
Data on labor performance and labor skill matrices (see image below) can assist APS systems in evaluating the skill sets of employees and automatically assigning tasks based on proficiency. This targeted approach to workforce deployment contributes to smoother operations and higher overall work order management efficiency.
5 Minimize Unplanned Downtime with Predictive and Periodic Maintenance
Manufacturers can employ predictive maintenance techniques, utilizing sensor data and analytics to foresee potential equipment issues before they lead to disruptions. As illustrated below, ML models can significantly reduce the risk of unexpected machinery failures, enhancing overall equipment reliability and contributing to the seamless execution of work orders, as highlighted by Deloitte.
About SCW.AI
SCW.AI offers a scalable cloud-based Digital Factory Platform designed to enhance manufacturers’ visibility, productivity, and agility. Our platform consolidates all production processes into a single interface, supported by our IoT Hub for streamlined high-quality data collection from the shop floor. We provide insightful reports and dashboards to empower decision-makers, and our AI algorithms, including those for scheduling, automate key decision-making processes.
To learn more about work order management and its digitalization do not hesitate to contact us.
To explore the full capabilities of SCW.AI’s Digital Factory Platform, book a demo now!