In today’s fast-paced manufacturing landscape, resolving immediate and chronic bottlenecks is a significant challenge without robust shop floor monitoring. The lack of visibility into operations often leads to prolonged issue resolution cycles, making it harder to reduce waste and improve productivity. This lack of transparency forces manufacturers to repeatedly tackle the same inefficiencies, stalling growth and innovation.
SCW.AI’s OEE Dashboard offers a transformative solution by providing real-time insights that make the hidden factory visible. This monitoring solution empowers the workforce—from operators to top management—to operate more efficiently, enabling a proactive approach to problem-solving.
In this article, we will explore the capabilities and benefits of SCW.AI’s OEE Dashboard, discuss its use cases across various roles, and answer frequently asked questions to help manufacturers unlock its full potential.
What is an OEE Dashboard?
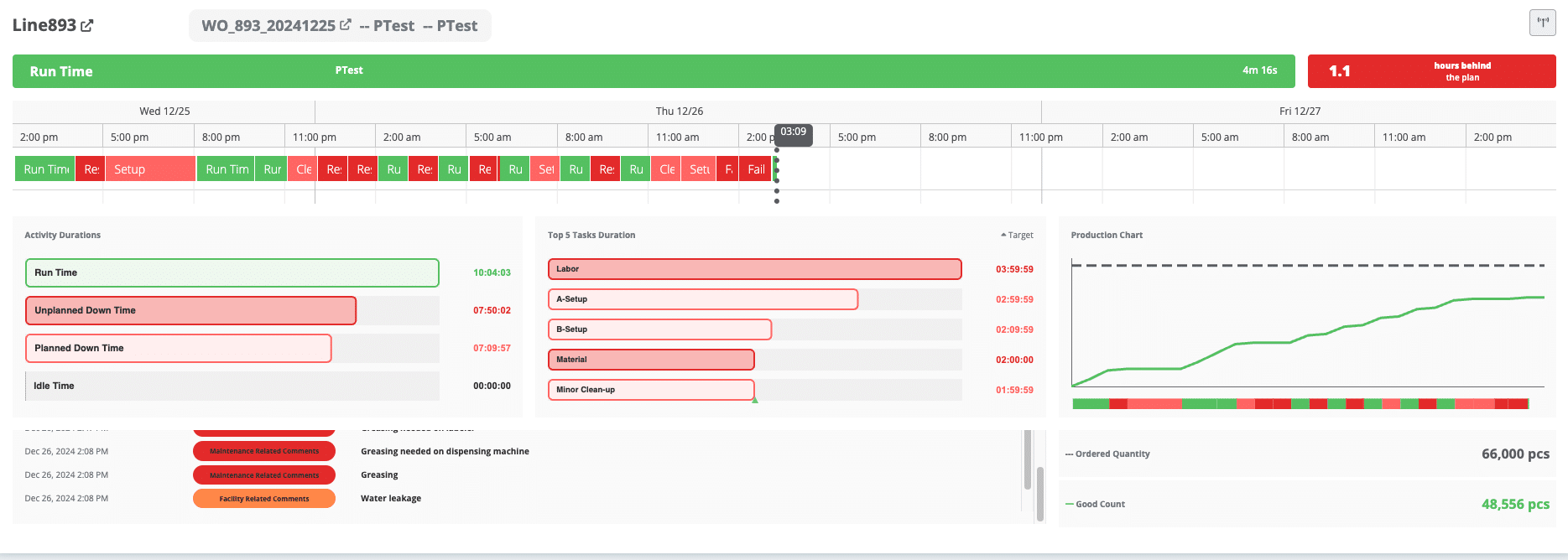
The OEE Dashboard is part of SCW.AI’s Digital Factory Platform, specifically the OEE Tracker Module, designed to empower manufacturers with real-time visibility into shop floor operations. It provides granular data, enabling workers to make informed decisions. By visualizing the status of lines and machines—whether idle, experiencing unplanned downtime, undergoing changeovers, or in run phases—the OEE Dashboard delivers actionable insights. Crucial manufacturing KPIs like OEE, cycle time, actual production vs. targets, and more are displayed for seamless monitoring and analysis.
One of the core strengths of the OEE Dashboard is its adaptability to the needs of various roles within the manufacturing ecosystem. For example:
- Line leaders can compare actual production against targets for their assigned lines and make adjustments, such as optimizing machine speed, to address potential delays.
- Executives can view site-wide operations, enabling them to reallocate resources for effective line balancing and overall optimization.
Another standout feature is the OEE Dashboard’s user-friendly interface. For instance, downtime events are immediately highlighted in red, making it easy to identify issues at a glance. Additionally, the OEE Tracker Module sends alerts and notifications for predefined scenarios. If a line experiences downtime, notifications are sent to the responsible line leader and relevant executives, facilitating prompt resolution.
OEE Dashboard vs. Excel Spreadsheets
Despite advancements in manufacturing technology, many facilities still rely on legacy methods like Excel sheets and paper-based systems. However, these traditional approaches fall short when compared to the capabilities of an OEE Dashboard:
- Real-Time Data: Unlike Excel spreadsheets, which rely on manual data entry and typically reflect previous day’s data, OEE Dashboards capture real-time shop floor data through IoT devices, PLCs, or OPC connections, enabling immediate action on emerging issues.
- Automation: OEE Dashboards automatically collect and display data, eliminating the time-consuming and error-prone process of manual entry and formula application in Excel.
- Role-Based Access: OEE Dashboards tailor information to specific roles. For instance, line leaders see only the data they need to manage operations, avoiding the confusion of site-wide information meant for higher management. This role-based design not only enhances efficiency but also supports a zero-trust security model for data protection.
- Alerts and Notifications: Unlike Excel, OEE Dashboards can send instant notifications. For example, if unplanned downtime occurs, key personnel are alerted immediately, enabling faster issue resolution.
Top 5 Benefits of an OEE Dashboard
1. Monitor Your Factory in Real-Time
The OEE Dashboard provides automatic updates, delivering the latest insights from the shop floor. Manufacturers gain a clear view of whether operations are progressing towards desired targets. For example, a daily production dashboard compares actual production counts with targets in real-time. Visual aids, such as a red line indicating the achievable output by the end of the day versus a purple line representing the production target, highlight discrepancies. If the red line falls below the purple line, it signals that the line is operating below its ideal takt time, prompting immediate action to meet goals.
2. Gain Deep Insights with Granular Shop Floor Data
The OEE Dashboard supports detailed analysis, offering insights at various levels to match the depth of the investigation:
- Global View: Displays overall OEE and the number of active lines across factories in multiple locations, enabling managers to assess high-level performance.
- Site View: Provides a visual representation of a specific factory, showing OEE and the status of each line, including worker check-ins.
- Line View: Offers detailed insights for individual lines, comparing actual and target durations for activities like pre-run, run, and post-run phases.
- Station View: Breaks down a line into individual stations or machines, displaying metrics like cycle time and first-pass yield. This granular perspective helps identify specific equipment or stations that degrade overall line performance.
3. Cut Operational Costs
With its ability to highlight both immediate issues and chronic bottlenecks, the OEE Dashboard helps manufacturers optimize processes and reduce waste. Chronic bottlenecks can be addressed through lean manufacturing strategies, agile practices, or total productive maintenance. Case studies reveal that manufacturers using OEE Dashboards can gain one to three days of productive time per week, significantly reducing costs while maintaining or exceeding pre-dashboard production outputs.
4. Enhance Workforce Collaboration
The OEE Dashboard facilitates seamless data flow across all organizational levels, from operators to top management. This transparency ensures that operator challenges are visible and acknowledged, fostering a collaborative environment where different departments align on solving bottlenecks. By using real-time data as a shared reference point, teams can coordinate efforts more effectively and resolve issues faster.
5. Drive Consistent Quality Improvements
As an integral part of quality management maturity programs and world class manufacturing initiatives, the OEE Dashboard monitors key metrics like scrap rates, good count numbers, and downed equipment in real-time. This information enables manufacturers to take a data-driven approach to continuous improvement, striving for maximum quality with every production cycle.
How Different Roles Utilize OEE Dashboards in Factories
1. Operators
Operators benefit from the OEE Dashboard through streamlined workflows and real-time access to essential data:
- Streamlined Data Entry: In cases where there are no OPC/PLC connections, operators can manually input line statuses directly into the system.
- Machine Configuration Efficiency: They can check critical machine settings such as target speeds and adjust operations accordingly.
- Problem Resolution: When issues arise, operators can use integrated chat functions to quickly request assistance, report issues, or clarify instructions from line leaders or maintenance teams.
- Efficiency Monitoring: With instant feedback on production metrics, operators can identify and correct deviations, ensuring operations stay on track.
- Training and Improvement: The dashboard can also be a learning tool, allowing operators to understand the impact of their actions on OEE and take ownership of their performance.
2. Line Leaders
Line leaders rely on the OEE Dashboard to maintain oversight and optimize their lines:
- Comprehensive Monitoring: Real-time tracking of OEE values (including data on availability, performance and quality), production speeds, actual vs. target production, first-pass yield, and the status of individual stations enables proactive decision-making.
- Intervention and Adjustment: They can intervene as needed, such as increasing machine speeds to keep production on track.
- Predictive Problem Solving: Early identification of trends, such as slow production rates or unusual number of items requiring rework, can be a harbinger of unplanned downtime. In such situations they can communicate with maintenance personnel, allowing line leaders to address potential issues before they escalate.
- Data-Driven Communication: Line leaders can engage with executives more effectively by presenting data-backed insights and updates, fostering clear and active communication.
- Shift Handover Efficiency: The dashboard provides a seamless transfer of information between shifts, ensuring continuity and reducing downtime during transitions.
- Simplified Reporting: Generating daily, weekly, or monthly reports becomes effortless with the dashboard’s real-time data updates, providing accurate and up-to-date insights.
3. Executives
Executives leverage the OEE Dashboard for informed decision-making and strategic oversight:
- Real-Time Granular Insights: By accessing site-wide and line-specific data, executives can quickly assess productivity and identify underperforming areas.
- Resource Allocation: They can reassign workers or shift resources between lines to balance takt times, ensuring production flows evenly across the site.
- Proactive Communication: Executives collaborate with line leaders to resolve bottlenecks, provide guidance on machine configurations, and ensure daily production targets are met.
- Strategic Adjustments: Decisions such as rescheduling lines, repurposing resources, or initiating overtime can be made swiftly to meet On-Time In-Full (OTIF) commitments and avoid costly penalties.
- Scenario Planning: By analyzing data trends, executives can anticipate bottlenecks and demand spikes, and adjust operations accordingly.
- Operational Transparency: With access to detailed metrics, reporting to top management becomes efficient and precise, allowing executives to focus on strategic improvements.
4. Top Management
Top management benefits from the OEE Dashboard through high-level visibility and data-driven insights for strategic decision-making:
- Performance Monitoring: With a single glance, they can evaluate the productivity and performance of multiple sites, enabling informed conversations with site managers about bottlenecks and resource needs.
- Capacity Planning: Improved visibility into the actual capacity of each site helps in making informed decisions about accepting new clients, managing stock levels, or scaling production.
- Strategic Expansion: The dashboard provides insights into whether new lines, machines, or facilities are needed to meet growing demands.
- Data-Driven Resource Allocation: Management can make better decisions about reallocating resources, optimizing labor, and investing in new technologies to enhance overall efficiency.
- Risk Mitigation: By identifying trends and recurring issues across sites, management can proactively implement strategies to avoid disruptions and maintain consistent output.
- Customer Satisfaction: Better visibility into production performance improves OTIF scores with time ensuring that client commitments are met, enhancing reputation and trust.
SCW.AI’s OEE Dashboard: A Game-Changer for Smart Manufacturing
The OEE Dashboard from SCW.AI is a highly versatile solution designed for ease of implementation, enabling deployment in a short timeframe. Its real-time data gathering and interpretation capabilities make it an ideal starting point for manufacturers embarking on full digital transformation initiatives.
Recognizing the evolving needs of manufacturers, SCW.AI designed the OEE Tracker as a scalable solution. While it can operate as a standalone tool, it seamlessly integrates with other modules from the SCW.AI Digital Factory Platform, such as Labor Tracker, Action Tracker, Scheduler, and more. This modular approach ensures manufacturers can expand their digital ecosystem over time, unlocking new capabilities and use cases as their needs grow.
The synergy between these modules amplifies the impact on efficiency and productivity. According to the World Economic Forum, many manufacturers going for end-to-end digitalization achieve around 40% reduction in operational costs, a 1.5x increase in output and even more.
If you would like to learn more about the OEE Tracker or the Digital Factory Platform, we invite you to contact us today.
Ready to experience the full power of the Digital Factory? Book a demo now!
OEE Dashboard FAQs
What is OEE?
OEE, or Overall Equipment Effectiveness, is a key manufacturing performance indicator that details losses in productivity. Expressed as a percentage, 100% OEE represents maximum efficiency with zero losses. By highlighting time losses, OEE becomes a valuable metric for estimating revenue, output, costs, and profits.
How is OEE Calculated?
OEE is calculated using three factors:
- Availability: The ratio of actual production time to planned production time.
- Performance: The speed at which production occurs relative to its ideal speed.
- Quality: The proportion of good units produced compared to the total units.
The formula is:
OEE = Availability × Performance × Quality.
What Makes an OEE Dashboard Different from MES Platforms?
While MES (Manufacturing Execution System) platforms provide some shop floor data, they typically lack the granular, real-time insights offered by an OEE Dashboard. MES platforms focus on broader operations and may not monitor specific line or machine performance in detail. They are also:
- More expensive
- Longer to deploy
- Potential legacy risks
Can SCW.AI Display Metrics Beyond OEE?
Yes, SCW.AI provides an extensive range of manufacturing metrics through the Digital Factory Platform. These include:
- Production Metrics: TEEP, cycle time, changeover time etc.
- Maintenance Metrics: MTTF, MTBF, MTTR etc.
- Planning KPIs: Schedule adherence, schedule compliance, capacity utilization etc.
- Quality Metrics: First pass yield, scrap rate, and more.
How Quickly Can SCW.AI’s OEE Dashboard Be Deployed?
SCW.AI’s OEE Dashboard can typically be deployed in under two months if you need integration with existing digital infrastructure. For sites that need our IoT tools to gather real-time data this process tends to be shorter. We ensure a fast, straightforward implementation process, minimizing disruption to your operations.