First Pass Yield is a KPI in manufacturing that measures the quality and efficiency of production processes. A high first pass yield is associated with several operational benefits, including:
- Reduced material waste
- Lower labor costs
- Fewer quality-related compliance penalties
- Minimized cost of quality
- Enhanced OTIF and takt time performance
- Improved customer satisfaction
Despite its importance, our decade of experience in the manufacturing industry reveals that many manufacturers do not monitor first pass yield as a KPI. Even fewer integrate their digital factory transformation initiatives with efforts to improve first pass yield, missing out on significant opportunities for optimization.
In this article, we will define first pass yield, including its formula and calculation examples. We will then explore seven ways digital lean strategies can enhance first pass yield, driving better results in manufacturing operations.
What Is First Pass Yield?
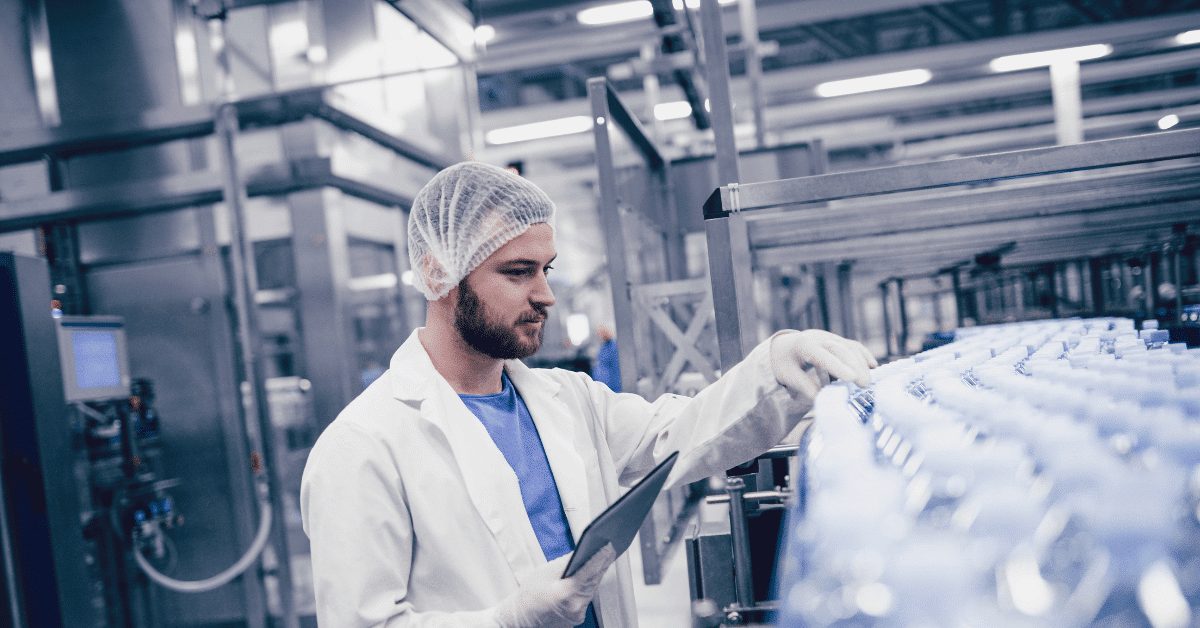
First Pass Yield, often abbreviated as FPY, is a key manufacturing metric that indicates the quality and efficiency of the production process. It is expressed as a percentage, with 100% representing perfect production quality—meaning no scrap, defects, or rework are necessary, and all products are completed in a single cycle.
However, any deviation from 100% FPY suggests that additional production cycles are needed to meet quality and quantity standards. In such cases, some goods may require rework or reproduction, leading to increased costs related to:
- Raw materials
- Labor
- Energy
- And equipment depreciation.
Moreover, low FPY can result in On-Time In-Full penalties due to delayed deliveries. If a manufacturer chooses to compromise on quality on the other hand, this can harm brand reputation and lead to penalties for failing to comply with industry quality standards.
4 Steps to Calculating First Pass Yield
Calculating first pass yield can be accomplished in four straightforward steps:
- Determine Time Interval for Analysis: Start by selecting the time period you wish to analyze for production quality, such as the last day, the previous week, or a custom date range that best represents your business need.
- Find Total Quantity of Production: Identify the total number of units produced during the chosen time interval, including all items, whether they are acceptable, defective, or require rework.
- Determine Number of Scrap and Units Requiring Rework: Calculate the number of units that are either completely unusable (scrap) or require rework before they can be sent to customers. This step helps isolate the defects within the production process.
- Insert Numbers Into the First Pass Yield Formula: Use the FPY formula, which is calculated by subtracting the number of defective units (scrap and those needing rework) from the total number of units produced. Then, divide this result by the total number of units produced and multiply by 100 to express the yield as a percentage.
First Pass Yield Calculation Example
Imagine you produce 1,000 goods for a work order. Of these, 34 products require rework, while 26 are scrapped and discarded. In this case, the first pass yield is 94%, as shown in the solution in the image below.
Discover our comprehensive Manufacturing KPIs Handbook, featuring detailed explanations and formulas for more than 60 key performance indicators, including first pass yield. Grab your copy now!
What Is a Good First Pass Yield Percentage?
A FPY percentage over 95 is generally considered a good score, while a FPY above 90% is typically seen as acceptable. However, these benchmarks might be misleading for heavily regulated industries. For example, in the pharmaceutical sector, manufacturers should aim for a 100% FPY because any deviation from quality standards can pose serious risks to human health and may lead to FDA warning letters and penalties due to non-compliance with cGMP (current Good Manufacturing Practices) regulations.
Top 7 Ways to Improve First Pass Yield in the Era of Digital Lean
1. Automate Calculation of FPY With Real-Time Data
To improve any metric on the shop floor, manufacturers must be able to monitor it in real-time with ease. Without real-time visibility, it becomes nearly impossible to take immediate action against events that reduce first pass yield and to identify chronic bottlenecks that require targeted remedies.
To display FPY in real-time on a report or OEE dashboard, manufacturers need to automatically collect data on the total number of products processed at a line, machine, or station during a selected time period, along with the corresponding counts of scrap and rework units.
Typically, machines with OPC connections can automatically collect such data. However, if these solutions are not available on the shop floor, IoT devices can be deployed for data collection:
- One device at the beginning of the line or machine to count the number of products or parts entering.
- Two devices at the exit—one to count scrap units and another to count units requiring rework.
Additionally, when monitoring quality and speed metrics, it is beneficial to display data at the machine or station level rather than for the entire production line. This granularity helps pinpoint specific issues, as a quality problem at one station can degrade the overall quality and speed of the entire line by preventing the flow of quality units to subsequent stations.
For instance, our Station View Dashboard is designed with this rationale. It shows FPY and cycle time in real-time at the machine level, providing line leaders and executives with detailed, actionable insights.
To find more information on OEE Tracker which has solutions such as Station View, Line View, Site View, Global View, OEE Waterfall Analysis and more click the button below.
2. Monitor Production, Lines and Environment
Various factors can significantly impact production quality and, consequently, first pass yield. These include:
- Heat and Humidity of the Production Environment: For example, one of our clients discovered that if the temperature of the production area falls below 25 degrees Celsius, FPY drops dramatically.
- Heat, Vibration, and Electric Current of Machines: Machine performance is closely tied to factors such as heat and vibration, with excessive levels leading to increased scrap production. Similar correlations may exist with fluctuations in electric current.
- Production Speed of Machines or Lines: Exceeding optimal production speeds can lead to a lower FPY, as faster operation beyond certain thresholds can compromise quality.
To maintain high FPY, these factors should be closely monitored. Ideally, real-time alerts or intelligent automation solutions should be in place to trigger preventive actions when deviations are detected.
For instance, as shown in the image below, Histogram Analysis can be a simple yet effective way to examine the historical distribution of heat and humidity data. By correlating these environmental factors with production KPIs, manufacturers can establish threshold values. IoT devices can be programmed to alert managers when temperatures exceed or fall below acceptable ranges, prompting HVAC systems to automatically adjust to maintain ideal conditions.
Similarly, when an operator sets machines to run faster than usual, AI-based anomaly detection systems can alert line leaders, requiring approval through alerts to ensure that such changes are intentional rather than setup errors.
Digital twins of factories offer a cutting-edge solution for monitoring and optimizing production values. By analyzing historical batch data and simulating potential scenarios with AI, digital twins can identify the optimal operational and environmental parameters for maximum FPY. They can automatically take corrective actions, such as adjusting heating and cooling systems or sending alerts when deviations from the golden batch occur.
3. Improve Your Total Productive Maintenance with Digital Tools and ML
Machine performance is closely linked to first pass yield. For instance, if a component of a machine fails, the station may continue to operate for hours, but it could produce units that require rework. Therefore, monitoring real-time machine-related data on dashboards—including metrics such as heat, vibration, mean time to failure (MTTF), mean time to repair (MTTR) and more—is essential for manufacturers to understand the correlations between these factors and FPY as well as improving total productive maintenance activities.
By establishing threshold values, deviations can be promptly communicated to the maintenance team via mobile devices, tablets or smartwatches, including alerts for unplanned downtime, enabling them to address issues quickly and maintain optimal machine performance.
Monitoring equipment and maintenance data also allows manufacturing professionals to develop proactive maintenance schedules, intervening before equipment falls below its peak effectiveness while it is still producing high-quality units.
In the era of Industry 4.0, the most effective way to schedule maintenance activities is by leveraging machine learning models for predictive maintenance. Although the model shown below focuses on maximizing runtime, similar models can be developed with other objectives, such as maximizing first pass yield. Such digital total productive maintenance strategies help producers to become world class manufacturers.
4. Standardize Tasks With Digital Forms
A study by the Boston Consulting Group highlights that manufacturing leaders consider digital Standard Operating Procedures (SOPs) to be as crucial as predictive analytics for ensuring top-notch production quality.
This emphasis on digital SOPs can be attributed to two key reasons. First, Digital Forms allow manufacturers to attach work instructions and checklists to various tasks—ranging from changeovers and machine setups to maintenance tasks and quality control. Moreover, such tools notify users automatically when a production result is out of specification. This standardization ensures that all activities are performed consistently and correctly, minimizing variability and errors.
Second, as noted in a McKinsey study on attracting Gen Z to the manufacturing workforce, this generation tends to prefer video-based solutions over reading text when troubleshooting. Considering that Gen Z is projected to make up one-third of the U.S. labor force by 2030 and is already an influential demographic, Digital Forms that support video attachments can play a vital role in the training processes for younger employees. Also, paperless manufacturing solutions help address the labor shortage in manufacturing by making the industry more appealing to Gen Z, as they align with the digital tools and technology this generation prefers.
5. Adhere Maximum and Minimum Waiting Time Constraints Between Processes With AI Schedulers
To achieve maximum production quality, it is crucial to manage waiting times between production processes, ensuring they stay within specified minimum and maximum thresholds. Adhering to these time constraints can be challenging, particularly in job shop scheduling, where multiple variables and dependencies must be managed simultaneously.
Advanced planning and scheduling systems now enable schedulers to define these constraints and other requirements. AI models then run your selected optimization scenarios such as just-in-time scheduling, changeover minimization, cost reduction with all subject to constraints. Thus, Schedulers help manufacturers improve first pass yield.
6. Assign Operators via Skill Matrices
Another strategic approach to improving first pass yield is to implement data-driven labor scheduling. Operators have varying levels of experience and proficiency with different tasks or types of products; for example, some may excel at specific operations like machine setup. By assigning workers based on their effectiveness for particular tasks and product families, manufacturers can enhance both production quality and efficiency.
Labor Skill Matrices are valuable tools that provide a clear visual representation of which operators have experience with specific tasks or products. As shown in the image below, darker colors indicate a greater proficiency with production of certain products, enabling managers to make informed decisions when assigning tasks.
7. Utilize Generative AI for Training Sessions
As mentioned earlier, operator errors in machine setups or deviations from SOPs can lead to a reduction in first pass yield. Also, manufacturers can now attach documents, images, and videos to Digital Forms to aid in training and adherence to SOPs.
Generative AI (GenAI) offers a powerful solution for creating training materials without the need for excessive time and resources. Manufacturers can quickly generate written documents, visuals, and instructional videos by providing clear prompts and iteratively guiding the GenAI with feedback to refine the content.
Furthermore, generative AI allows manufacturers to customize training materials in formats preferred by different workers. For instance, as discussed earlier, Gen Z may prefer video content, while older generations might find text-based materials more effective. By leveraging generative AI, manufacturers can create diverse training resources that cater to the varied learning preferences within their workforce, ultimately supporting greater quality and performance.
To learn how digital transformation assists European pharma manufacturers on reaching 100% FPY and beyond that closing productivity gap, download our Bridging Europe’s Pharma Productivity Gap with Digital Factory Transformation eBook!
Maximize Your FPY with SCW.AI
Our Digital Factory Platform is an end-to-end cloud manufacturing solution that helps manufacturers maximize production quality and efficiency through real-time data, dashboards, intelligent automation, and paperless quality solutions. It includes modules such as:
If you want to learn more about first yield pass and how you can maximize quality of production with our solutions, contact us.
To experience our Digital Factory Platform firsthand, book a demo now.